Electrical Steel Engineering and Technologies
Lamination Solutions for Superior Performance
Design & Engineering
Our design and engineering services can help you exceed expectations with advanced engineering support, metallurgical expertise, and skilled tool makers. Let us help you achieve your product development goals.
Tooling & Quality Production
Our precision tooling delivers tight tolerances, extended die life, and cost-efficient manufacturing. With in-house tool design, global tool sourcing, and fully equipped tool maintenance rooms, Tempel helps ensure your product’s a success.
Material Selection & Purchasing
Tempel is a global leader in electrical steel laminations. With more than 75 years of experience in global steel sourcing, we’ve established a reputation for expertise and reliability in sourcing, processing, and testing electrical steel.
Progressive Stamping
Minimize waste and reduce assembly costs with progressive stamping. Our team can design and build progressive tooling to meet your exact specifications, from the initial strip layout to the selection of steel and carbide components.
Annealing
Our innovative annealing capabilities bring the latest technologies in electrical steel laminations to our customers. Annealing improves the magnetic performance of lower-cost materials, making them a viable alternative to more expensive high-alloy grades.
Core Assembly
Tempel's core assembly services can help you get your motors and transformers up and running faster. We offer a range of capabilities, including interlocking, gluing, welding, and bonding. We can also recommend post-stamping value-added services to improve magnetic properties.
Bonding
Cut the risk of interlaminar shorts with Tempel's bonding capabilities. Offering both glue dot and full surface bonding, we can provide the ideal bonding method for your lamination cores.
Prototyping
Tempel's electrical steel prototyping services are the blueprint for success for any engineer or manufacturer looking to bring their next great product to market. With our help, you can quickly and easily create samples of your electrical steel components to validate the design and performance before mass production.
Die Casting
Whether in the automotive, aerospace, electronics, or other industries, Tempel’s aluminum die casting has been a cornerstone for our manufacturing facilities , offering unmatched benefits in terms of strength, cost-effectiveness, and design flexibility.
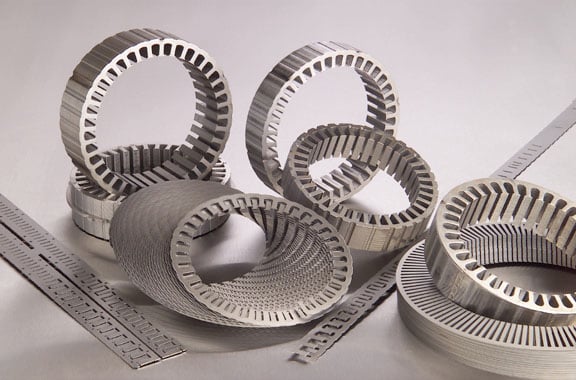
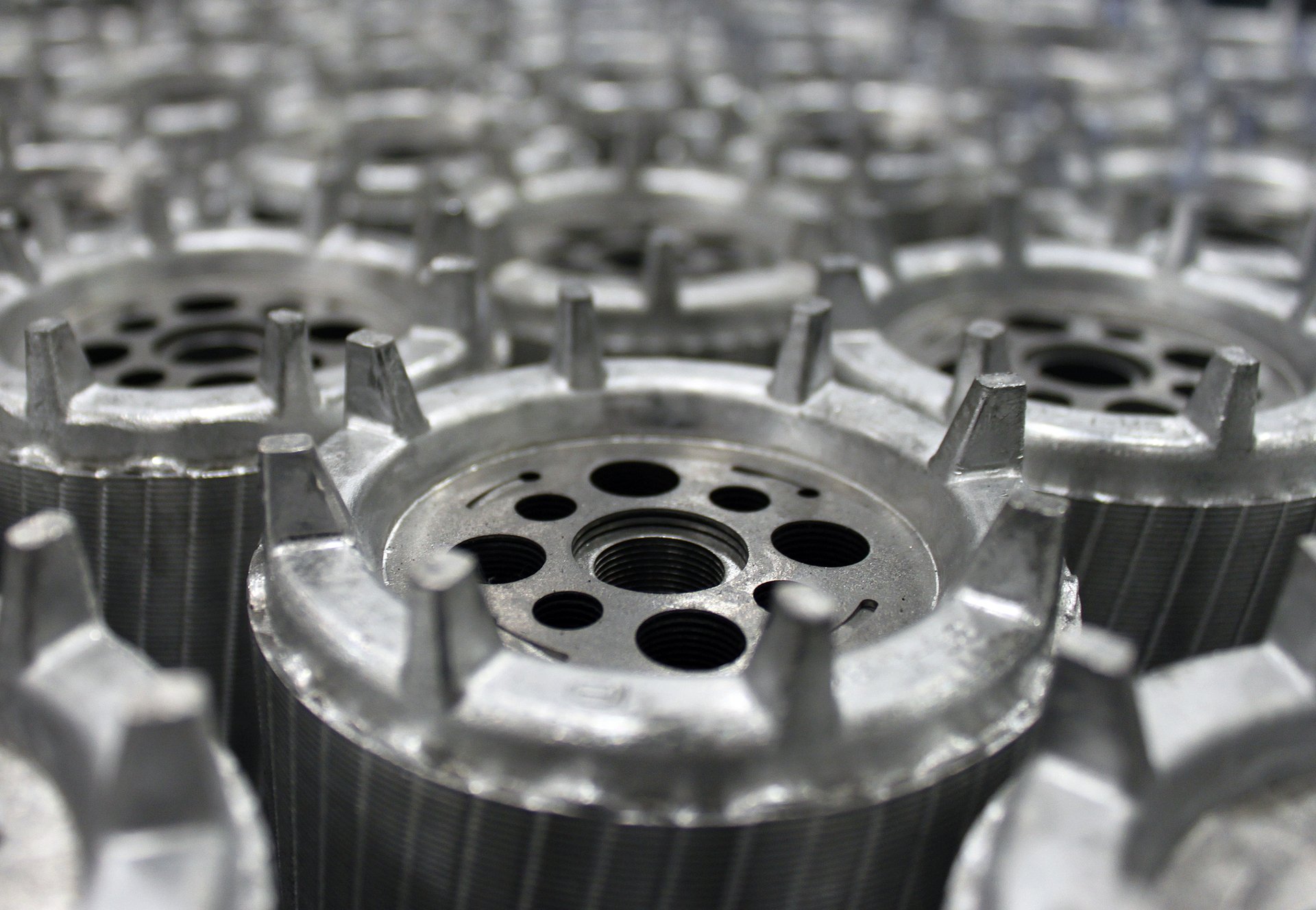
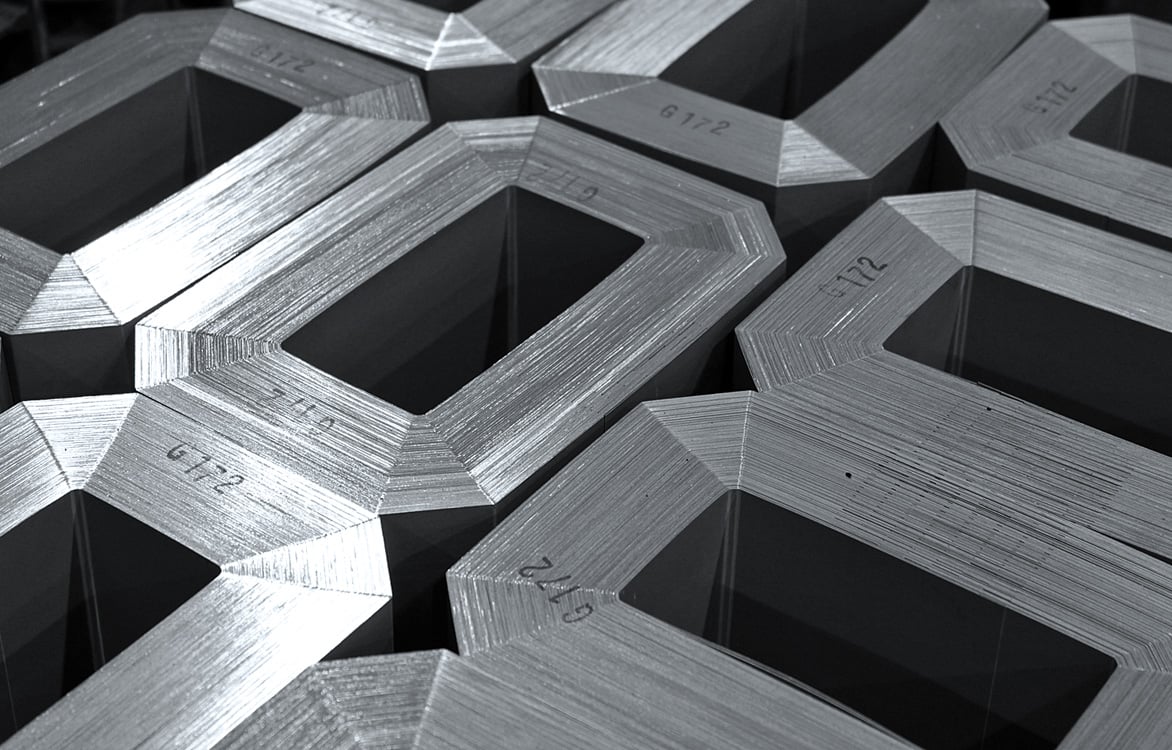
Precision Stamping Products Layered with Quality
Discover Your Electrical Steel Solution with Tempel
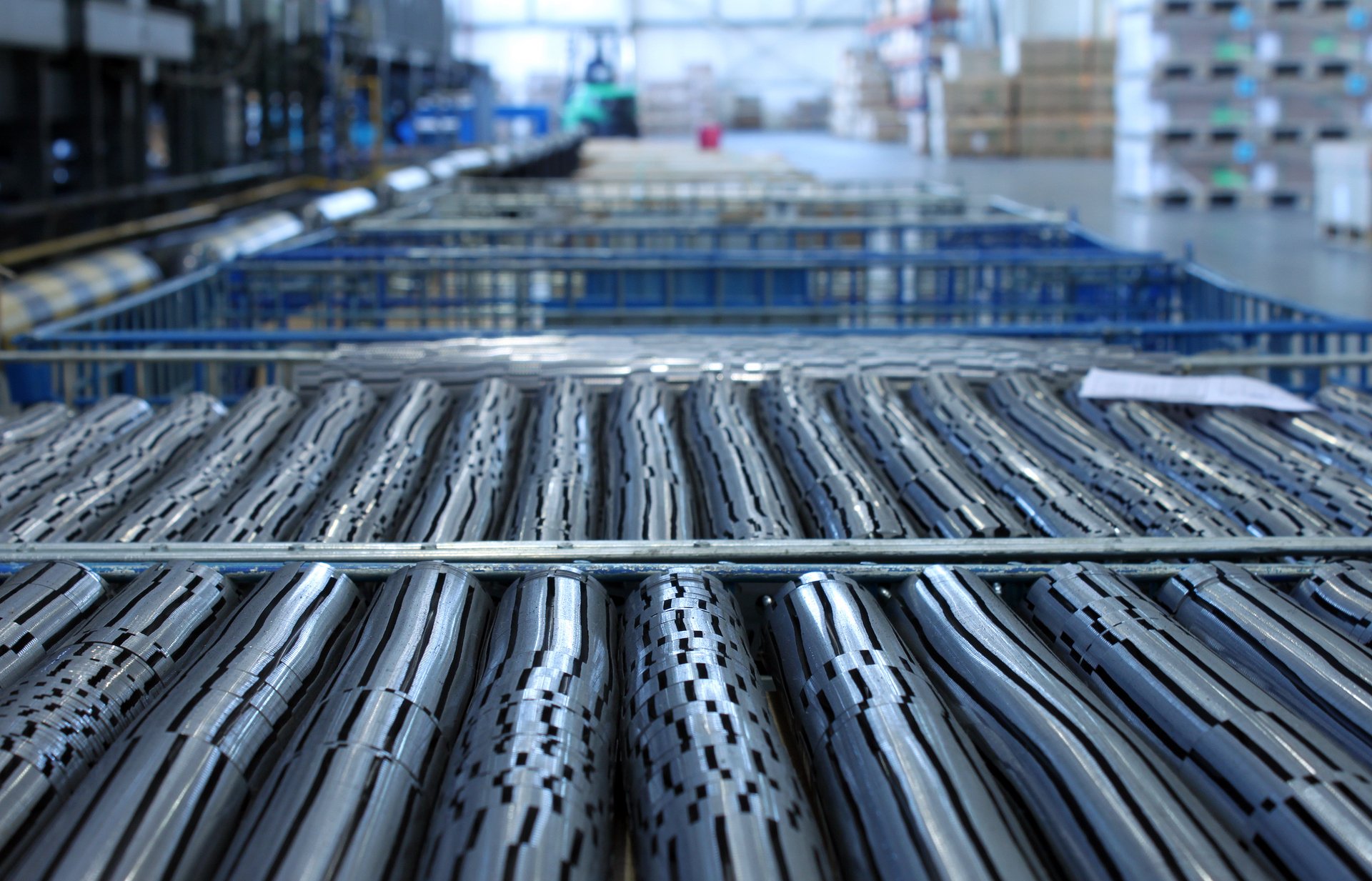