Aluminum Die Casting
The Power of Aluminum Die Casting
Whether in the automotive, aerospace, electronics, or other industries, Tempel’s aluminum die casting has been a cornerstone for our manufacturing facilities, offering unmatched benefits in terms of strength, cost-effectiveness, and design flexibility. Tempel expertise in die casting of rotor cores, adds conductor bars and end rings to induction motor rotors. Similarly, we use the same process to add damper bars and end plates to generator rotors. The sophisticated process provides high quality rotor cores that are ready to go into the motor core assembly process. Tempel die casts not only both loose laminations and interlocked cores, with and without skewing but also provides added processes such as burnishing, reaming, gate compression and/or removal, flash removal, and rotor OD machining.
When it comes to squeeze casting and centrifugal casting for applications where minimal porosity is required, Tempel has the experience and technology to provide the right solution.
Cost Effective
The die casting process can be highly automated, leading to lower labor costs and higher production rates. Tooling costs can be high initially but are amortized over the production life of the die, making it cost-effective for large quantities.
High Strength-to-Weight Ratio
Despite its lightweight nature, aluminum die castings offer excellent strength and durability, making them suitable for a wide range of structural applications.
Excellent Thermal Conductivity
Aluminum has good thermal conductivity, making it suitable for components that require efficient heat dissipation, such as heatsinks in electronics.
Precision and Complexity
Die casting allows for the production of intricate and complex parts with tight tolerances, reducing the need for additional machining or assembly operations.
Corrosion Resistance
Aluminum has inherent corrosion resistance, which can be further enhanced with various surface treatments or coatings.
Die Casting Process
Interlocking
If not using an interlocked core, core assembly is required first. This includes measuring the correct amount of laminations, disorientation for gamma purposes, skewing, and pinning of the rotor core.
Die Casting
Molten aluminum is forced into the rotor core in the die cast mold.
Separation
Gate plate is separated from the rotor core and sent back for reuse.
Processing
Rotor cores made with loose lams are de-pinned and then move on for added processing.
U.S. patents or foreign patents may apply to this method for the product. Please visit here for more information.
Explore Related Services
We're more than an electrical steel laminations supplier; we're a strategic partner in the quest to optimize your products. With our leading-edge solutions in processing, stamping, and engineering, we can help you improve product performance, efficiency, and reliability.
Ready to connect with Tempel’s team of experts?
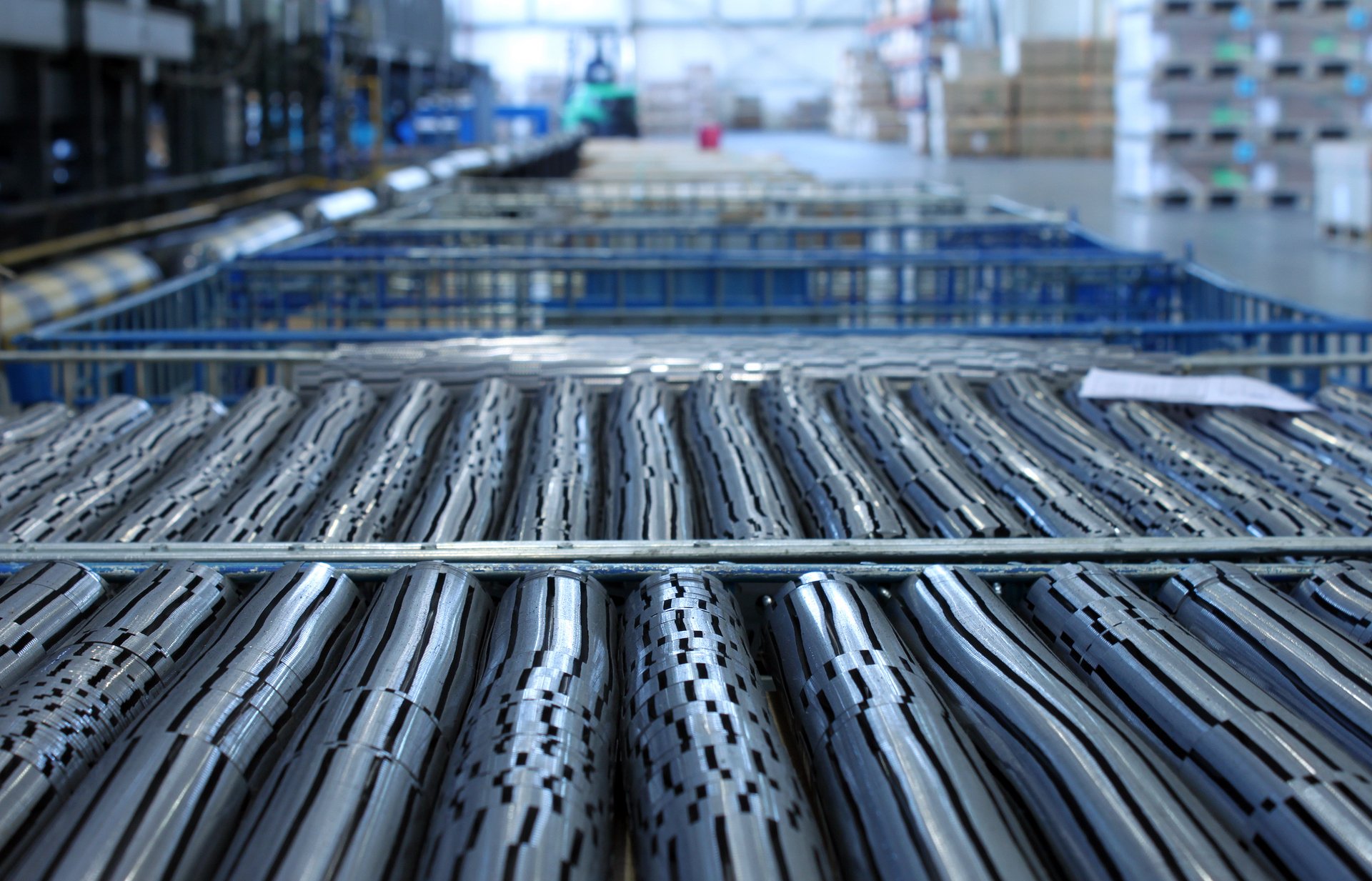