Electrical Steel Sourcing
Global Electric Steel Sourcing for Laminations
Tempel has been in the electrical steel stamping business for over 75 years, and we know what it takes to produce the highest quality electrical steel laminations. We source our material from the best suppliers in the world, and we use a custom-designed gamma tester to ensure every master coil meets our strict standards for cross-width thickness and shape profile. Our expertise and reliability in assessing potential suppliers, negotiating prices, and establishing contracts has made us a trusted partner for customers in the e-mobility, transportation, industrial, and energy sectors.
Global Steel Vendor Relationships
Our global network of steel vendors gives us the flexibility to source a wide range of electrical steel types, even in times of supply chain uncertainty. Our long history and strong relationships mean you can rely on us to deliver the steel you need when you need it.
Metallurgical Knowledge and Expertise
We are the electrical steel sourcing and metallurgical experts for Non-Grain Oriented (NGO), Grain Oriented (GO), and Cold Rolled Motor Lamination (CRML) steel, with the knowledge and resources to help you select, buy, and source the right material for your application.
Electrical Steel Sourcing Quality Assurance
Before any steel is accepted at our facilities, we subject it to a battery of tests, including a custom-designed gamma tester, Epstein testing, and other raw material evaluations. Our rigorous quality assurance process ensures that we utilize nothing but the best materials.
Statistical Process Control
Our process is focused on quality. We conduct detailed reviews and audits to ensure continuous adherence to quality improvement assessment and VDA6.3 requirements. We use InfinityQS statistical process control software to collect, integrate, monitor, analyze, and report on data in real time, allowing us to tightly control our processes.
Strategic Steel Sourcing, Selection, Purchasing & Processing
Identify Needs and Establish Preferred Suppliers
We work with our customers to pinpoint their electrical steel needs, whether they're looking for non-grain oriented (NGO) or grain oriented (GO) steel. We then forge a strategic sourcing plan that ensures you get the right steel at the right price, on time.
Develop a Sustainable Sourcing Portfolio
When you rely on a single supplier, any disruption can bring production to a halt, and even a small difference in quality can have a major impact on performance. That's why it's critical to develop a sourcing portfolio that ensures access to uniform, high-quality steel with equivalent performance in all global regions.
Evaluate Raw Materials and Continuously Monitor Quality
Our rigorous testing of raw steel materials ensures that final products conform to our customers’ specifications.
Monitor and Mitigate Supply Chain Risks
Our risk mitigation process keeps your supply chain running smoothly, even in the face of unexpected challenges. Our team of experts is constantly monitoring the market and making adjustments to ensure that we have a steady supply of high-quality electrical steel for our customers.
U.S. patents or foreign patents may apply to this method for the product. Please visit here for more information.
Explore Related Services
We're more than an electrical steel laminations supplier; we're a strategic partner in the quest to optimize your products. With our leading-edge solutions in processing, stamping, and engineering, we can help you improve product performance, efficiency, and reliability.
Ready to connect with Tempel’s team of experts?
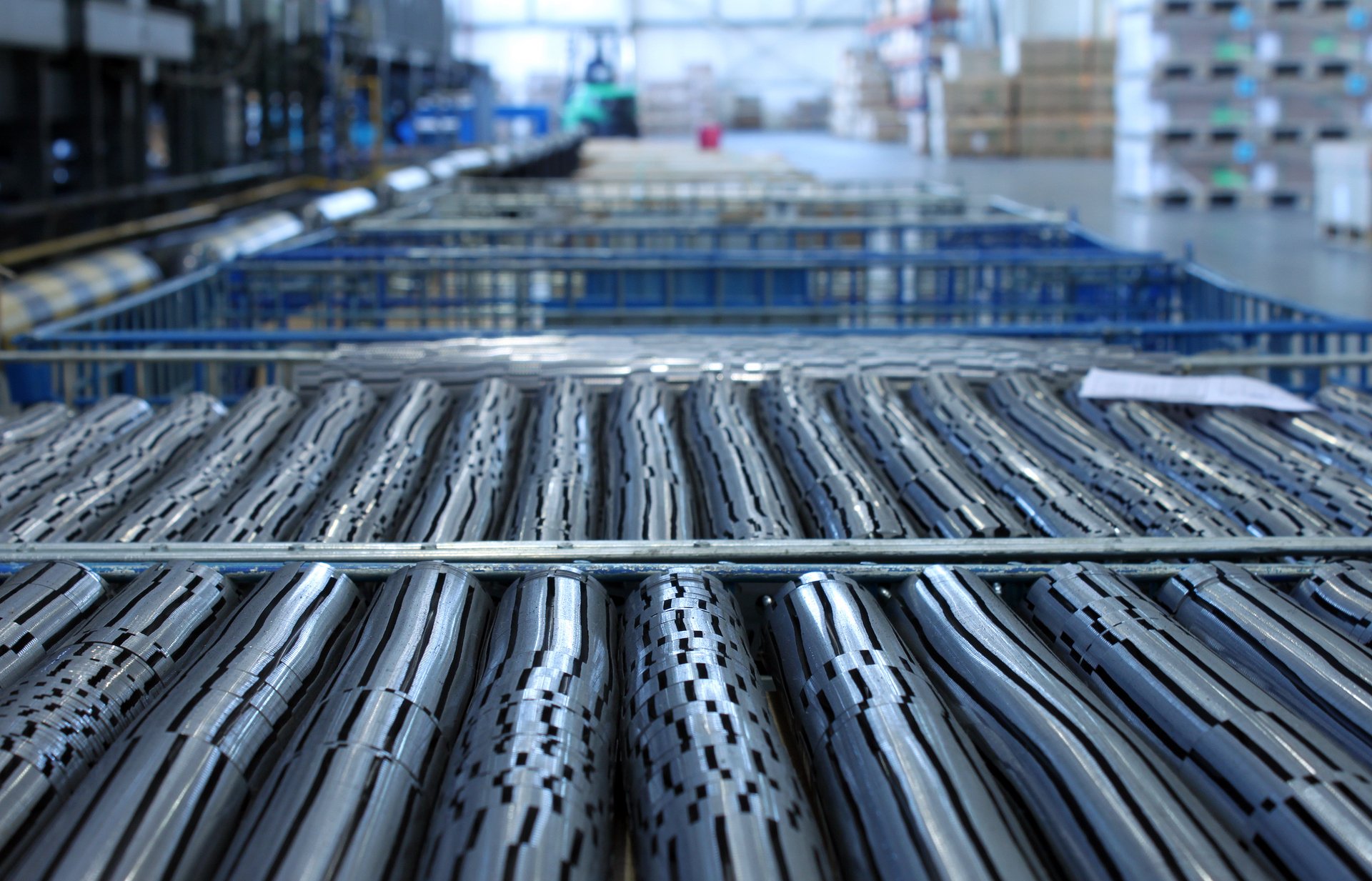