Core Assembly
Unitize Laminations with State-of-the-Art Core Assembly Processes
Get ready-to-use unitized cores that boost your motor and transformer assembly. Tempel's core assembly services take the hassle out of assembling your product. We offer a range of capabilities, including: interlocking, gluing, welding, and bonding. We can also recommend post-stamping value-added services to improve your cores' magnetic characteristics.
Reduce Production Cycle Time
Our streamlined core assembly capabilities are designed to accelerate your production. We deliver ready-to-use motor or transformer cores in efficient time frames, so you can get your products to market faster.
Decrease Equipment and Labor Costs
Tempel's core assembly services give you the peace of mind that your cores will be built to the highest standards—without the need to add in-house assembly capabilities and personnel.
Value-Added Services
Boost the magnetic characteristics of motor and transformer cores with our post-stamping annealing capabilities.
Comprehensive Core Assembly Capabilities
Explore our range of core assembly offerings
Interlocking
Our cost-effective unitization process allows for numerous design features, including indexing and multiple-part geometries. Interlocking allows for post-stamping annealing, and while it has limitations in both diameter and stack height, it’s a versatile and efficient way to unitize products.
Welding
Our MIG, TIG, pulse TIG, and laser welding solutions can create strong, reliable cores from loose laminations, interlocked sub-stacks, and full interlocked stacks. We can even add vent laminations to improve motor cooling for larger cores. Our welding process allows for post-stamping annealing both before and after welding, ensuring cores are strong, durable, and high performing.
Full Surface Bonding
Laminations made from steel strips are coated with a bonding adhesive. After stamping, the cores are fixed and the adhesive cured with heat and pressure. The resulting cores exhibit unparalleled dimensional characteristics, structural integrity, and feature an interlaminar seal that prevents leakage in liquid cooling applications.
In-Die Bonding
Glue dots, applied as the strip progresses through the die, adhere individual laminations together once they are punched from the strip. This process can limit press speed and reduce the ability to run multi rows, and it does not allow for post-stamping annealing.
U.S. patents or foreign patents may apply to this method for the product. Please visit here for more information.
Explore Related Services
We're more than an electrical steel laminations supplier; we're a strategic partner in the quest to optimize your products. With our leading-edge solutions in processing, stamping, and engineering, we can help you improve product performance, efficiency, and reliability.
Ready to connect with Tempel’s team of experts?
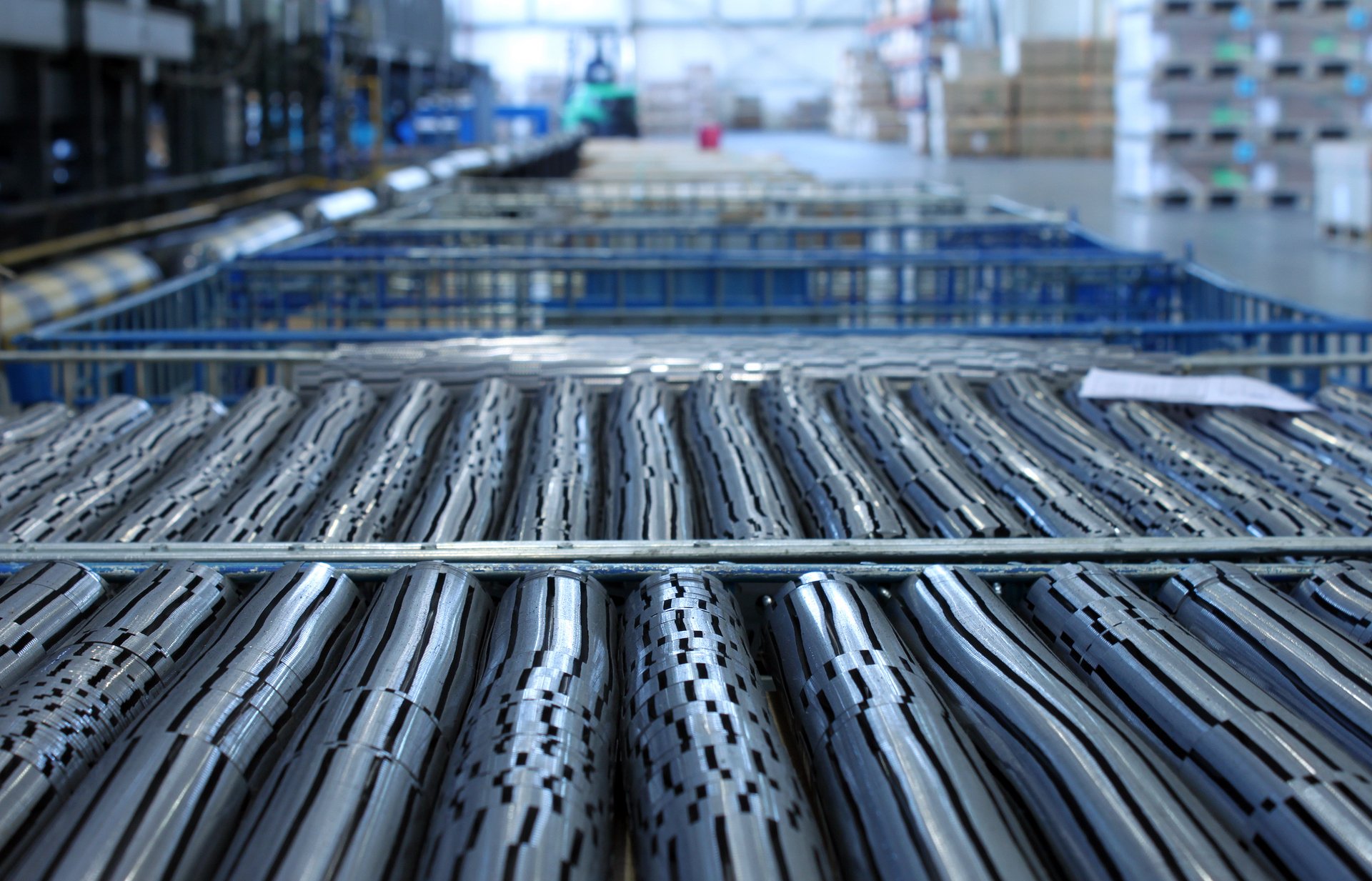